The Asian Coal Ash Association was founded to bring together industry, academia, governments, NGO’s and other stakeholders in the utilization of coal combustion products . The AsianCAA aims to promote initiatives of a scientific, technical, industrial, environmental, educational and legal nature associated with applications for coal ash produced from Asian coal fired power stations.
The Association endeavours to achieve these aims through:
- Holding of exhibitions, meetings, lectures, classes, seminars and training courses in the usage of coal ash, e.g. pulverised fuel ash(PFA), furnace bottom ash (FBA), cenospheres, etc.
- Representing the members on international, national and regional standard committees .
- Providing of datasheets, literature and information to interested parties.
- Sponsoring and promoting research into new applications and developments which utilise coal ash.
- Developing collaborative initiatives and projects that support commercial solutions for the utilization of coal ash.
Anyone who has an interest in coal ash products – ranging from specifiers, users, hauliers, suppliers, researchers, etc – are welcome to join as Associate Members. Strategic and Principal membership are also available for industry leading organizations.
Please visit our Membership page for more details.
Newsfeed
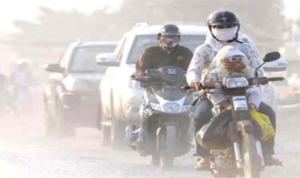
power plants, coal ash, clean coal, environmental policy, reform, Viet Nam
Asiancoal Ash
Comment
power plants, coal ash, clean coal, environmental policy, reform, Viet Nam
Asiancoal Ash
Comment
Coal Ash Waste Increases in Viet Nam
power plants, coal ash, clean coal, environmental policy, reform, Viet Nam
Asiancoal Ash
Comment
power plants, coal ash, clean coal, environmental policy, reform, Viet Nam
Asiancoal Ash
Comment
power plants, coal ash, clean coal, environmental policy, reform, Viet Nam
Asiancoal Ash
Comment
power plants, coal ash, clean coal, environmental policy, reform, Viet Nam
Asiancoal Ash
Comment
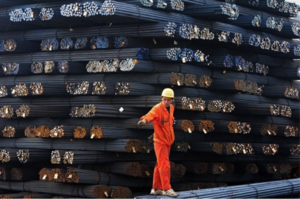